Ultimate Guide to Pipe Relining Techniques
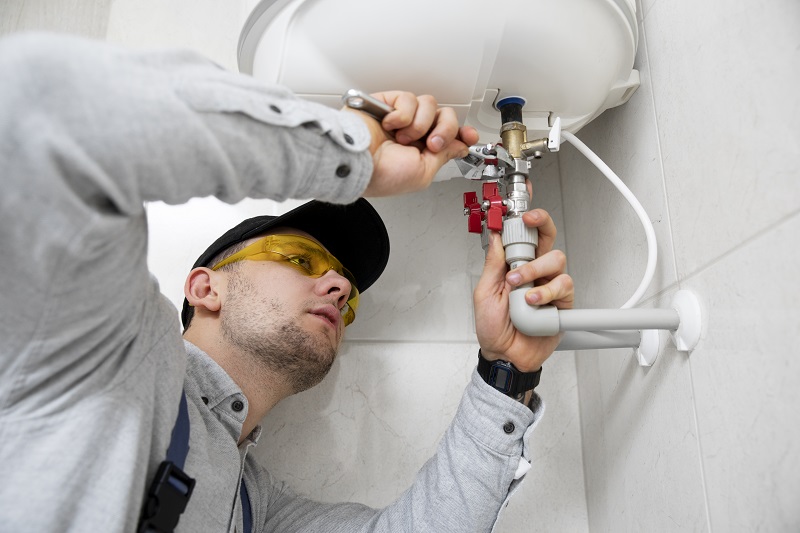
Have you ever wondered if there’s a way to fix your ageing pipes without digging up your entire garden? Are you frustrated by repeated blockages or unpleasant smells coming from your drains? Do you worry about the costs of excavating your property just to replace a few damaged pipes? If these questions sound familiar, you’ve come to the right place.
In this post, we’ll explore all things pipe relining—especially how it’s transforming the plumbing scene in Potts Point. We’ll talk about everything from the basics of no-dig solutions to detailed methods like Cured-In-Place Pipe (CIPP) lining. Plus, we’ll look at some frequently asked questions, cost considerations, and tips on finding a reliable contractor in Australia.
By the time you’ve finished reading, you’ll have a thorough understanding of pipe relining and why it’s such a popular choice for both commercial and residential properties. Whether you’re battling tree root intrusions or looking to prolong the life of your existing drainage lines, you’ll discover that pipe relining offers an excellent alternative to traditional pipe replacement methods. Let’s jump right in!
Understanding the Importance of Pipe Relining in Potts Point
Potts Point is a vibrant suburb with a mix of historic buildings and modern developments. Beneath those charming facades, however, lies a complex network of ageing pipes that can cause all sorts of headaches when they fail. This is precisely why pipe relining has gained so much traction in the area. It offers a long-running solution that reinforces existing pipes from the inside, essentially creating a new pipe within an old one.
The concept is straightforward: instead of digging up entire sections of your property, professionals use a specially designed liner that’s inserted and then hardened in place. This delivers a durable barrier against leaks, cracks, and root intrusions. As Potts Point’s buildings get older, the stability of underground infrastructure becomes more critical than ever. By opting for pipe relining, property owners can preserve their landscaping, walkways, and building exteriors without compromising on effectiveness.
Moreover, this approach is often faster and cleaner than large-scale excavation. With minimal downtime, Potts Point residents can quickly resume their day-to-day activities. It’s a method that aligns perfectly with the area’s pace of life—fast, efficient, and respectful of tradition.
The Growing Popularity of No-Dig Solutions
The term “no-dig solutions” refers to methods that replace or restore underground pipes without turning your property into a construction site. In places like Potts Point, this is a game-changer. Close-knit living spaces and heritage-listed buildings require careful measures to protect surfaces and landscaping.
No-dig solutions don’t just save your garden; they also shorten repair times and reduce labour costs. These modern techniques rely on ingenious engineering and high-grade materials designed to last for decades. They meet Australian standards, providing peace of mind that you’re benefiting from proven technology. In many cases, you’ll also find that pipe relining can handle everything from small pinhole leaks to more serious structural issues.
What’s more, no-dig solutions minimise the noise, dust, and disruption experienced with traditional digging. Instead of having a team of workers on-site for days, you can often get back to normal within hours. For Potts Point homeowners who value their time, this is a major plus. It’s fair to say that as awareness grows about how plumbing pipes can be restored from the inside out, no-dig solutions continue to gain momentum as the sensible way forward.
Pipe Relining vs. Traditional Pipe Replacement
Property owners in Potts Point often wonder: Is relining really worth the hype? Is it better than ripping out the old pipes entirely? The answer usually depends on the situation, but pipe relining frequently emerges as the more attractive option.
Key Differences in Method and Outcome
Traditional pipe replacement involves digging up the damaged sections, physically removing them, and fitting brand-new pipes. This is effective but can be time-consuming and may require re-landscaping. By comparison, pipe relining skips the heavy digging and instead builds a strong new pipe inside the old one. The outcome is a leak-proof, durable pipeline with minimal property disruption.
Advantages and Drawbacks of Each Approach
One major advantage of traditional replacement is that it allows you to fully inspect the ground underneath your pipe network. However, the drawbacks include higher labour costs and the risk of collateral damage to driveways, gardens, and foundations. Pipe relining, on the other hand, is often cheaper and quicker. One downside is that severely collapsed pipes might be beyond relining repair, but that’s not very common.
Cost Comparison: Short vs. Long-Term
While pipe relining may sometimes seem pricey up front, it tends to be more cost-effective if you factor in long-term savings. Avoiding excavation means you don’t have to spend money restoring landscaping or driveways. Also, the ongoing stability of a newly lined pipe can mean fewer repair bills in the future. Traditional replacement might appear cheaper in certain cases, but with hidden restoration costs, it can quickly add up.
Overview of Pipe Relining Techniques
Relining isn’t just one method; there are several approaches that come under the “no-dig” umbrella. Each technique suits different pipe conditions and property requirements, making it crucial to select the right one.
Cured-In-Place Pipe (CIPP) Lining
CIPP lining is a popular approach that involves inserting a resin-saturated tube into the damaged pipe. Once in place, the lining is inflated so it sits snugly against the pipe walls. Heat or UV light is then used to harden, or “cure,” the resin. This results in a seamless, joint-free new pipe that resists leaks and blockages. Because it’s versatile, CIPP is often the go-to choice among Australian plumbers.
Inversion Lining
Similar to CIPP, inversion lining also uses a pressurised inversion drum that turns the liner inside out as it travels through the pipe. This ensures the resin-coated side is always against the damaged pipe walls. It’s effective when dealing with bends or diameter changes. Once the liner is fully inverted, heat or ambient curing sets the resin in place.
Pull-in-Place Lining
As the name suggests, this method involves pulling the liner into position through the existing pipe. Technicians will usually install a calibration tube to maintain proper pressure. This method is particularly helpful if you only need to reline a specific section of pipe rather than an entire run. Pull-in-place reduces material usage while still providing a strong, watertight result.
Pipe Bursting and Related Methods
Though slightly different from relining, pipe bursting is often mentioned in the same “no-dig” conversation. With pipe bursting, a bursting head breaks apart the old pipe while simultaneously pulling through a new one behind it. It’s handy if your existing pipe has collapsed in several places. Like other techniques, pipe bursting cuts down on large trenches, though you’ll still need small access points.
Step-by-Step Guide to the Pipe Relining Process
If you’re curious about what actually happens during a pipe relining job, here’s a concise outline of the main steps. Although the specifics can vary by technique, these stages generally remain consistent across most methods.
Initial Inspection and Assessment
First, technicians run a CCTV camera through the pipe to identify issues like cracks, corroded spots, or root intrusions. This inspection also helps them decide which relining method is most suitable. The condition of the pipe, its diameter, and any bends or joints will factor into this decision.
Cleaning and Preparation
Next, the pipe must be thoroughly cleaned. High-pressure water jetting clears debris, roots, and any build-up. A clean interior ensures the resin can bond effectively to the pipe walls. If there are stubborn obstructions, mechanical cutting tools might be used before the relining begins.
Installing the Liner and Curing
Once the pipe is clear, the lining material—saturated with resin—is inserted. Depending on the technique, it might be inflated or inverted using air pressure. The curing process then hardens the resin, turning it into a solid, seamless barrier. Heat or UV lights are commonly used to accelerate this step.
Post-Relining Inspection and Verification
After curing, technicians perform another camera inspection to confirm that the new liner is properly in place and free of wrinkles. They’ll also check that all branch lines are open, ensuring your property’s drains perform optimally. Once everything looks good, the pipe is put back into service.
Cost Considerations and Value
Cost is usually top of mind for property owners. With pipe relining, you’re investing in a lasting repair that safeguards your home or business from further damage.
Typical Pipe Relining Costs in Australia
Pricing can vary widely based on pipe length, diameter, and accessibility. On average, pipe relining in Australia ranges from a couple of thousand dollars for shorter sections to tens of thousands for extensive commercial projects. Keep in mind that while the cost seems high, it’s often more economical once you factor in avoided excavation.
Long-Term Savings and Return on Investment
One of the best features of pipe relining is how it eliminates the need for constant maintenance. By creating a like-new pipe, you minimise future blockages and leak risks. This means fewer repairs over time, which translates into tangible savings for homeowners and businesses alike.
Comparing Financing and Payment Options
Many plumbing contractors provide flexible payment plans or financing options. This allows customers to spread the cost over manageable monthly instalments. Investigating these options can make the decision to reline much easier, especially for larger properties or commercial sites.
Maintenance and Preventative Measures
Even the best relined pipes benefit from routine attention. Simple checks and preventive steps can help your relined pipes stand the test of time.
Aftercare Tips for Newly Relined Pipes
Once your pipes are relined, try to keep corrosive chemicals out of the drains. Also, avoid flushing items like wet wipes or sanitary products. Although your new liner is tough, good habits will extend its life and keep everything flowing smoothly.
Common Mistakes to Avoid
A common mistake is ignoring small warning signs, assuming the relined pipe will never need another look. While relining is exceptionally durable, it’s still wise to address any small issues before they escalate. Also, be cautious about DIY drain cleaners that might damage the interior lining over time.
Scheduling Routine Inspections
Professional inspections can catch early signs of wear or potential blockages. Many property owners arrange annual or bi-annual check-ups, especially if their pipes are prone to tree root intrusion. This small investment goes a long way in preserving the health of your relined system.
Commercial vs. Residential Pipe Relining
While the basic principles remain the same, commercial and residential properties have distinct considerations. Understanding these can help you pick the right service approach.
Special Considerations for Businesses
Businesses often can’t afford extensive downtime. As a result, the fast, minimal-disruption nature of pipe relining is a winner for commercial settings. In larger facilities, multiple pipe runs may need relining, so scheduling and phasing the work carefully is crucial to keep operations flowing.
Council Approvals and Australian Regulations
Some relining projects—especially those involving main lines or shared drains—require approval from local councils or utility providers. It’s vital to check these regulations in advance. Smooth coordination with local authorities helps ensure your project meets all Australian safety and environmental standards.
Coordinating with Property Managers
For strata or rented properties, involving the property manager early on can save time. They can communicate with tenants and help obtain necessary approvals. A clear relining plan keeps everyone on the same page and minimises complaints about noise or interruptions.
Addressing Potential Client Pain Points
Pipe relining can raise concerns about cost, quality, and inconvenience. Here’s how a well-executed project tackles these issues head-on.
Minimising Disruption to Your Property
The core advantage of pipe relining is how little it disturbs your daily life or business operations. By using existing access points, contractors avoid excessive noise, dust, and equipment. This approach preserves landscaping, floors, and walls, saving you the hassle of post-project clean-ups and repairs.
Ensuring Quality and Longevity
Quality control matters. Contractors use high-grade epoxy or polyester resin that’s designed to resist corrosion and root intrusion. Post-lining CCTV inspections confirm a perfect fit. Some companies also provide final reports and video footage so you can see the newly lined pipe for yourself.
Balancing Costs and Benefits
While the initial quote for pipe relining can appear daunting, it’s important to think about the bigger picture. Excavation projects involve not just the plumbing work but also the cost of putting your property back together. When you balance that against a one-time relining expense, most people find the value proposition speaks for itself.
Conclusion
Summing up, pipe relining isn’t just a buzzword—it’s a tried-and-tested method changing how Potts Point residents and businesses deal with failing pipes. Rather than resorting to a full-blown excavation, you can now transform old, damaged lines into reliable, leak-proof channels that stand the test of time. Plus, you’ll steer clear of the extensive disruptions and cosmetic repairs that come with traditional pipe replacement.
Ultimately, if you’re noticing slow drains, recurring blockages, or suspect root invasion, now is the time to explore pipe relining. Get in touch with knowledgeable contractors who can do a thorough CCTV inspection and provide a transparent quote. Don’t forget to ask about financing options, warranties, and their experience with no-dig methods. By taking these simple steps, you’ll protect your property’s plumbing, save money in the long haul, and enjoy peace of mind knowing your pipes are in excellent condition—even beneath the beautiful streets of Potts Point.