Strength and Versatility: How to Choose the Best 4130 Tubing for Aerospace and Automotive Applications
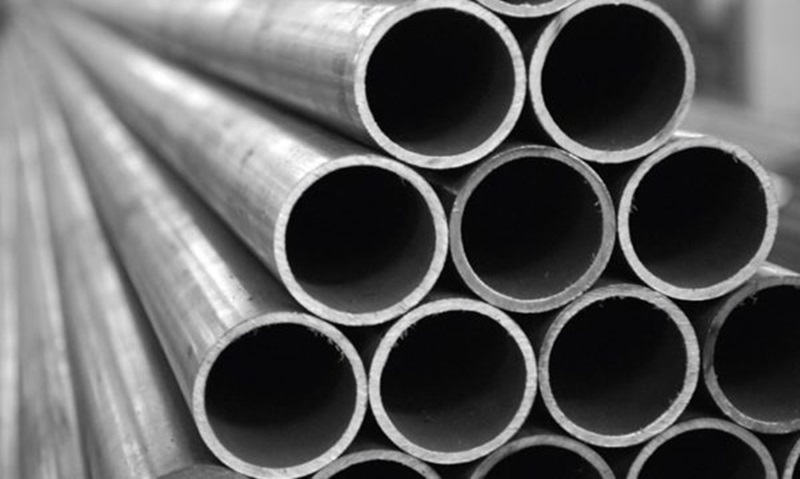
4130 tubing, also known as chromoly tubing, is a highly regarded alloy steel characterized by its blend of chromium and molybdenum. It is celebrated for its exceptional strength-to-weight ratio, robustness, and versatility, making it a preferred choice in demanding fields like aerospace, automotive, and performance cycling. The alloy’s unique composition offers superior tensile strength and toughness while providing good fatigue resistance. Its weldability and adaptability to various forms of heat treatment further enhance its appeal.
In aerospace and automotive engineering, the selection of materials is pivotal in determining the final product’s performance, durability, and safety. Among various materials, 4130 steel tubing, commonly known as chromoly tubing, stands out for its exceptional strength, versatility, and reliability. This blog post delves into the critical factors to consider when selecting 4130 tubing for aerospace and automotive applications, ensuring that your choice meets and exceeds these industries’ stringent demands.
What is 4130 Tubing?
4130 steel is an alloy made of chromium and molybdenum, earning it the moniker ‘chromoly.’ This combination imparts high strength, excellent toughness, and good resistance to fatigue, making it a prime choice for demanding engineering applications. Its unique properties have made it a staple in the aerospace and automotive industries, where performance and safety cannot be compromised.
Key Considerations in Choosing 4130 Tubing
-
Understanding Application-Specific Requirements
Aerospace Applications: Aircraft components must withstand extreme conditions and stresses. 4130 tubing is often used in constructing airframes and landing gear due to its high strength-to-weight ratio, enhancing performance without adding unnecessary weight.
Automotive Applications: In the automotive industry, especially in racing and high-performance vehicles, 4130 tubing is used for roll cages, chassis construction, and suspension components. Its ability to absorb impact and resist deformation under high stress is crucial.
-
Dimensional Precision
Tubing Size: The diameter and wall thickness of 4130 tubing are crucial before you buy 4130 tubing. In aerospace, precision is key, as the tubing must fit perfectly within complex assemblies. For automotive applications, the size will often depend on the desired strength and the weight considerations of the vehicle.
Customization: Many suppliers offer custom sizing, which can be essential for specific aerospace or automotive needs.
-
Mechanical Properties
Strength: 4130 tubing provides an excellent strength-to-weight ratio. Choosing tubing that can handle the expected load and stress is essential.
Toughness: This characteristic is particularly important in aerospace applications, where materials are subjected to extreme operational environments.
-
Weldability and Fabrication
Welding Considerations: 4130 tubing requires proper welding techniques to maintain structural integrity. Pre and post-weld heat treatment is often necessary.
Fabrication Flexibility: The ability to fabricate the material into complex shapes and forms is vital, especially in aerospace engineering, where component geometry can be intricate.
-
Corrosion Resistance
Protective Measures: While 4130 steel has some inherent corrosion resistance, additional protective coatings might be necessary, particularly in environments where exposure to corrosive elements is a concern.
-
Heat Treatment Compatibility
Enhancing Properties: Heat treatment can significantly improve the strength and hardness of 4130 steel. Understanding how tubing will respond to such therapies is critical for applications requiring enhanced properties.
-
Compliance With Standards
Certification and Standards: Ensure that the 4130 tubing meets the standards and certifications required in aerospace and automotive industries, like ISO, ASTM, or specific aerospace quality standards.
-
Supplier Reliability
Quality Assurance: The consistency in quality from your supplier cannot be overstated. This is vital for maintaining the integrity and safety of the final product.
-
Practical Tips for Selection
Research and Collaboration: Work closely with engineers and suppliers to understand the specific needs of your project.
Sample Testing: If possible, test samples of 4130 tubing under conditions similar to their intended use.
Cost-Benefit Analysis: While 4130 tubing may come with a higher cost than some alternatives, its benefits often outweigh the initial investment in the long run.
Conclusion
Selecting the right 4130 tubing for aerospace and automotive applications is a task that demands careful consideration, an understanding of material properties, and a keen eye on the specific requirements of the project. By considering factors such as strength, size, fabrication needs, and compliance with industry standards, you can ensure that the material not only fits the purpose but also contributes significantly to the overall success and safety of the project. Remember, in industries where the margin for error is minimal, the choice of material can make all the difference.
In summary, when it comes to choosing 4130 tubing, it’s not just about selecting a material; it’s about investing in the reliability, safety, and performance of sophisticated engineering marvels. Whether it’s soaring through the skies or speeding on the racetracks, with the right 4130 tubing, your project is poised for excellence.