How are Supplier Audits Conducted?
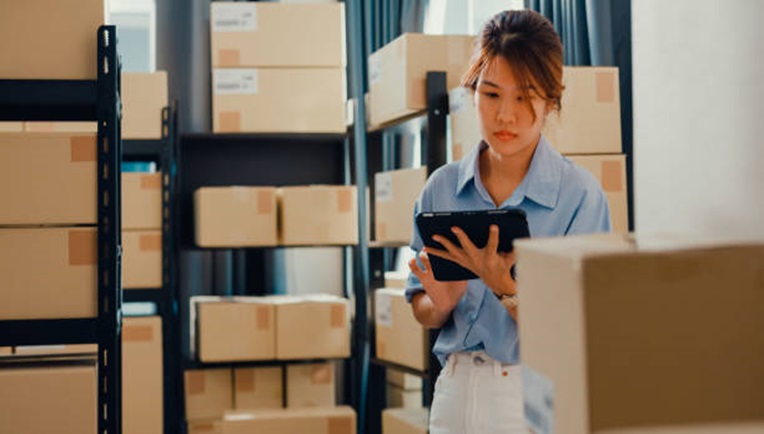
Supplier audits are crucial for ensuring quality assurance and compliance of the bought goods throughout your supply chain. It brings oversight and visibility to your supply chain, helping you detect and rectify mistakes early, thus preventing any issues down the road. So, let us see how a leading China inspection company conducts a supplier audit.
The Four Categories of Supplier Audits
The whole supplier audit process consists of four key categories that have a specific focus and ensure high standards of quality and performance across the supply chain.
- System Audits: This involves the evaluation of the effectiveness and efficiency of the management system as a whole rather than focusing on individual components. The leading China inspection company will examine the process, function, timing, personnel, and location of tasks within the supply chain as per the specified criteria. System audits provide a high-level view of your operations to help you understand any areas of your supply chain system that require improvement.
- Process Audits: These include a detailed evaluation of discrete steps within the supply chain. The auditor will evaluate each process step with attention to performance and outcomes related to the preceding stage. It will involve evaluating all the components required to create the finished product, including personnel, machinery, and raw materials. These elements are compared to guidelines, performance, measures, principles, and instructions.
- Product Audits: This category of audit involves examining the product against specifications before it is shipped to an end user or retail market. These specifications include aesthetic appearance, functional performance, and dimensional consistency. It determines whether a step in the production process is misaligned and needs retooling or if the quality system needs adjustment as a whole.
- Compliance Audit: While the above three categories of audits provide feedback to each other and are based on internally defined specifications, compliance audits focus on aligning the process and product specifications with written documentation, either by disqualifying or verifying. It determines whether or not specifications are met and requires conformity to an external specification that may require larger changes to the supply chain. Ethical audits, C-TPAT audits, environmental audits, and food safety audits are common types of compliance audits.
Types of Supplier Audits
Now, within these categories of supplier audits, there are various supplier audit programs, each of which helps you evaluate your suppliers’ adherence to different standards, including international regulations, product quality standards, or ethical standards. Let us see the various types.
- Ethical audits: These are compliance audits that check if appropriate work conditions are being applied. Regulatory standards or internally-mandated policies guide them.
- Manufacturing audits: These are conducted to ensure suppliers are manufacturing your products to your specifications and following the processes correctly.
- Structural audits: They are conducted in the supplier’s buildings to ensure that fire safety measures, structural integrity, and general building codes are being maintained.
- Living Wage Audits: These are compliance audits that check whether or not employees are receiving enough remuneration to afford a decent standard of living. They help clarify potential issues before they become serious problems.
- Environmental audits ensure compliance with regional, local, national, and international environmental standards and help with mitigation and remediation issues.
- Food supplier audits evaluate your supplier’s food handling quality and safety measures for good manufacturing practices and regulatory compliance.
- Chemical safety audits: These audits assess the potential chemical hazards against the control a company has put in place to eliminate the risk.
- C-TPAT Audits protect a company, suppliers, and customers from security threats by evaluating the current risk exposure and recommending securing the physical and digital assets.
The Process of Conducting a Supplier Audit
Supplier audit is a straightforward process but includes certain critical steps. A third-party auditor may provide you with the expectations for the audit by giving context and sharing knowledge during your initial meeting. They have a local presence in the manufacturing location. The supplier audit process has four main stages as follows:
- Opening Meeting: This includes discussing the objectives of the audit between the client, auditor, and audit program manager; establishing clear goals, expectations, and criteria for the audit; ensuring that the objectives align with the auditor’s capabilities and timeframe; and determining if any regulatory audit conditions are appropriate to include.
- Factory Tour: This will include conducting the audit through onsite inspection b, overviewing the facility and equipment conditions and creating a factory profile, and health and safety evaluation by inspecting the health and safety hazards, compliant information posting, and PPE accessibility. A major part of the factory tour is information gathering by providing detailed descriptions of products and processes examined through production capabilities, evaluation of QA systems, and workflow and organization charts.
- Employee Data Gathering: These are for only social compliance audits and include employee documentation reviews and interviews.
- Closing Meeting: This involves concluding the audit by comprehensive report submission, which will include the overview of objectives, findings, corrective action plan (CAP), discussion, and recommendations.
Look for a Reliable Third-Party Auditor
Since supplier audits protect your supply chain and customers from harm, you need to conduct them regularly by hiring reliable third-party audit and inspection services. This will guarantee consistency, compliance with the law, and the highest degree of quality excellence.