A Definitive Guide to How EMS Providers Can Lower Their PCB Rework Costs
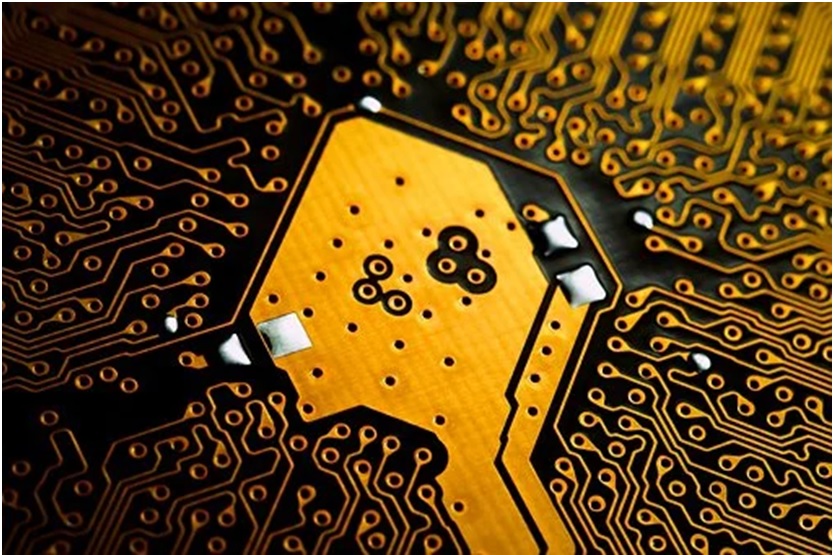
In PCB design and manufacture, the word ‘rework’ refers to any work that needs to be done after the printed circuit board (PCBs) have been assembled, and all manufacturing operations are complete. Rework tasks can be categorized into –
- There’s a need to fix an inherent problem in the PCB design. For example, the assembly operators may have selected the wrong resistor values or the wrong ICs.
- The PCB design needs to be changed for an explicit reason. For example, the EMS provider may need to switch out components from their PCBs that aren’t compliant as per modern standards to create new functionalities.
Contrary to popular belief, PCB rework and repair are two totally different beasts. PCB repair is required when the PCB fails for certain reasons. For example, there might have been too much solder applied to a PCB, causing it to short-circuit. Such accidental failures require PCB repairs.
On the other hand, the need for PCB rework implies mistakes at the design level. Or, the intended design may work perfectly, but it may not support the latest product requirements. So, PCB rework specialists have to re-adjust the design and create a reworked batch of PCB components.
PCB Rework – Addressing the Cost-Related Issues
PCB rework involves the use of heat and solder to conduct mechanical operations like cutting down traces. Skilled workers are required to modify the physical components. For small-scale EMS providers, these rework-related expenses can go out of control very quickly.
PCB rework requirements can cost these businesses thousands of dollars in monthly losses. So, why not avoid investing in PCB rework processes and scrap the defective boards altogether? Well, scrapping entire batches of printed circuit boards costs companies three times the annual costs of rework.
So, PCB rework procedures are almost always worth the money as the only alternative (scrapping the boards) is much more expensive. However, multi-layered, high-density PCBs are very difficult to rework.
To make sure these difficulties don’t overstretch manufacturing budgets, PCB manufacturers and EMS providers need to take three important steps. Here’s how they can lower their annual PCB Rework Cost –
-
Invest in Better Inspection Techniques
The best way for EMS providers to reduce the need for PCB rework is to set clear manufacturing standards at all facilities and have strong processes in place that make it easier to detect solder defects, opens/shorts, component defects, etc., early on. Although some defects will always be inevitable in multi-layered assemblies, efficient PCB inspection can help businesses reduce the constant need to send their boards for rework. Some inspection techniques EMS providers and PCB manufacturing companies need to invest in include –
- Automated Optical Inspection – Acquire high-speed automated pieces of machinery that can instantly detect anomalies like missing components on the PCBs. These automated inspection techniques are far superior to manual optical inspection processes.
- X-Ray Inspection Tools – It’s very easy to inspect leadless PCBs using these devices. Most modern-day PCB assemblers and manufacturers rely on manual x-ray inspection techniques.
- Automated X-Ray Inspection – AXI tools are slightly expensive, but they’re extremely efficient at spotting PCB defects.
If small-scale EMS providers or PCB manufacturing companies can’t set up such efficient PCB inspection systems inside their facilities, they can always cut costs by outsourcing these tasks to third-party experts. Just make sure that the third-party inspection companies employ workers who have received their IPC certifications. Following the IPC-A-610G guidelines, in particular, is extremely important for PCB inspection specialists.
-
Designing ‘Rework-Friendly’ PCBs
While designing the PCBs, manufacturers must ensure their design choices positively impact future rework procedures. PCB designers can significantly decrease the amount of rework their boards may require in case they have flaws by simply adopting design practices such as –
- Making the PCBs Larger in Size – Larger PCBs are easier to rework. They’re easier to place on benchtops. Probing for errors is also easier when you’re working with larger prototype PCBs.
- Make the Components Larger – Reworking super-small components are obviously more challenging than reworking larger components. So, make the components as big as possible and also make sure each component has ample space around. Without these spaces, processes like localized rework reflow heating would be extremely difficult and time-consuming.
- Programmable Parts – By adding simple and cheap programmable parts such as programmable microcontrollers or programmable voltage regulators, allow rework experts to reconfigure the PCB design without causing too much risk to the device in general. Programmable parts make rework procedures extremely flexible, so adding such components to the product prototypes (at least) is something all PCB manufacturers must consider.
PCB design choices influence the future rework of products, so make sure your design processes are “rework-friendly.”
-
Invest in Third-Party PCB Rework Specialists
Lastly, small-scale PCB manufacturers and EMS providers must consider outsourcing their rework responsibilities to certified third-party experts. In-house PCB rework procedures can over-stretch manufacturing budgets. Just imagine if a rework process goes wrong – the company will have to cover the costs of rework in addition to the costs of manufacturing completely new PCBs. The risk factors associated with in-house rework procedures are too big for some companies to handle. So, they must consider hiring third-party PCB rework specialists who –
- Use state of the art equipment.
- Employ IPC certified operators who can perform the rework and repair in accordance with the IPC-7711/7721 guidelines.
- Have prior experience reworking large PCB batches.
- Can guarantee fast and reliable services.
Finding such specialists of PCB rework and repair can help companies dramatically reduce their annual expenditures on rework procedures.