6 Easy Business Changes to Make Your Warehouse more Eco-Friendly
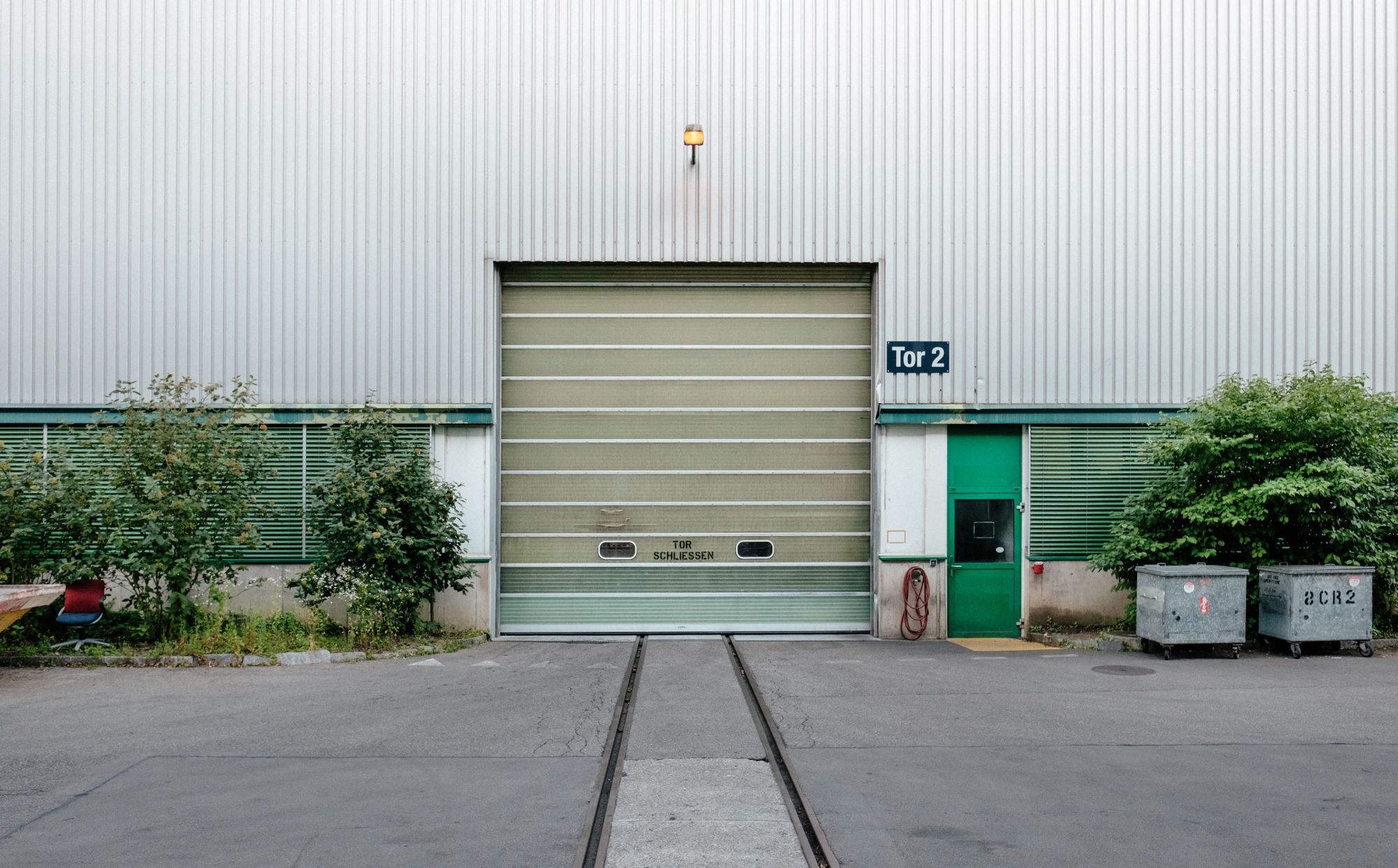
Warehouses aren’t known for being the eco-friendliest workplaces, but this is changing fast. Warehouse managers are looking into ways to turn their job sites into bastions of environmentally friendly work and here are some of the changes that they’re introducing.
1. Lighting sensors
In order for workers to be able to maneuver equipment and materials throughout the warehouse, they need adequate lighting. A well-lit room prevents many dangers such as slipping and bumping into dangerous machines. However, warehouses are very large areas and it’s unlikely that there will be a worker in every single area and on every corner. Because of this, a lot of lighting effectively becomes a waste of power.
To remedy this, you can install some simple switches and sensors that will reduce the amount of electricity used by the lightbulbs on the work floor. Whenever a worker enters a certain area, the light will turn itself on, and when they exit, it will go off to conserve power. The sensors aren’t difficult to set up and you get to reduce the amount of power that is wasted on a daily basis
2. Efficient regulation of temperature
Heating is one of the largest expenses in every warehouse. Good air conditioners can only do so much. You need to be able to keep the room temperature adequate for long periods of time in order for work to continue without issues. During winter months, you can expect that just keeping the heat at a tolerable level will cost you a lot of money.
A lot of warehouses aren’t properly insulated and they lose significant amounts of heat every single day. Better insulated windows and more efficient door systems could allow you to save quite a bit on the heating bill, which is why they should be considered.
3. Energy efficient machinery
There has been a lot of buzz around electrical machinery in the past couple of years, and for good reasons. Once upon a time, heavy machinery such as forklifts and cranes couldn’t run on anything except diesel and gas, which means they were forever doomed to be producers of pollution and harmful gases. Recent improvements in battery technology have allowed many of the most common warehouse machines to turn to electric sources instead of fuels.
Battery-powered forklifts are soon becoming the gold standard for eco-friendly warehouses. They can run for as long as a diesel-powered forklift can and they don’t need expensive fuel to keep running. Best of all, as battery technology improves, they can be made smaller and more maneuverable without sacrificing strength or lifting power.
4. Going paperless
Paper is a seemingly quintessential part of nearly every workplace. In warehouses, the paper has a lot of functions that are deemed essential. Workers need schedules and managers have to deal with a lot of paperwork to keep the business going. It also serves as a way to keep track of shipments and make sure that everything is being sent to its proper destination. Unfortunately, this creates a lot of paper waste that could be avoided.
A lot of modern warehouses are going paperless and making use of digital technology to stay ahead of their tasks and projects. There are a couple of benefits that go along with this. For starters, computers are a lot more reliable than paper. If a fire starts, you can count on the server to keep all the information safe on the cloud and you don’t lose anything. On the other hand, with digitalization, no paper is wasted and you help save a countless number of trees from being cut down.
5. Optimizing the floor layout
A lot of warehouses practice asset tracking to figure out the efficiency of transport within their facilities. The results often show that the work floor isn’t well-optimized for fast transport and efficiency. When workers and forklift drivers need to make dozens of turns to get to their destination, it’s going to slow down everyone in the building.
A good layout prevents this. It gives workers the ability to get assets from one end of the warehouse to its destination near transport vehicles without losing precious time. Dealing with stops and repairs also becomes easier. For well-optimized warehouses, Sitecraft and similar experts offer maintenance carts that are easy to maneuver and don’t take up a lot of space, which makes it easier for maintenance crews to get to machinery and repair it quickly without disrupting the flow of work.
6. Proper packaging methods
Every warehouse has to make use of packaging to secure assets and shipments. You can’t ship things out without a box to protect it. However, the material used for packaging isn’t exactly eco-friendly. A lot of packaging includes bits and pieces of plastic which isn’t exactly biodegradable. Efficient packaging methods allow you to cut down on unnecessary harmful waste.
Conserving as much material as possible is the goal. Alternatively, another way to cut down on harmful waste is to use a material that is considered biodegradable. While plastic-based packaging takes hundreds of years to break down, more biodegradable materials take only a short while and they can even be used as compost. This significantly reduces your warehouse’s carbon footprint and allows you to package things with a clear conscience.
Conclusion
Turning your warehouse from a polluting factor into an eco-friendly workspace isn’t easy, but it’s definitely a manageable task. Technology is paving the way for much more efficient work and much less waste and all you have to do is take advantage of it and reap the benefits.